EUA to 510(k) - Brace yourself, the tides turn again
Have you obtained EUA for your U.S. product?
Are you grappling with the ever-shifting landscape of quality and regulations?
Brace yourself as the tides are turning again.
Companies that have received EUA were not required to have complete quality system controls. The primary focus for EUA compliance was centered around the ability to take regulatory action for products in the market.
This means that the companies were required to account for distributed inventory, company registration and product listing, and complaint handling to identify and address reportable events and recalls where needed.
However, these facets only scratch the surface of a comprehensive quality system. The U.S. Food and Drug Administration (FDA) is ushering companies with EUA products toward a 510(k) submission for FDA clearance.
With this transition comes an upsurge in regulatory obligations, invoking the stipulations of 21CFR 820 and necessitating a fully compliant Quality Management System (QMS).
You need a system that’s compliant but also works for you and not the other way around.
That’s where we can help. At MDC, we’ll help you make sense of the many elements required for a comprehensive and compliant QMS implemented in a practical way that propels rather than hinders your progress.
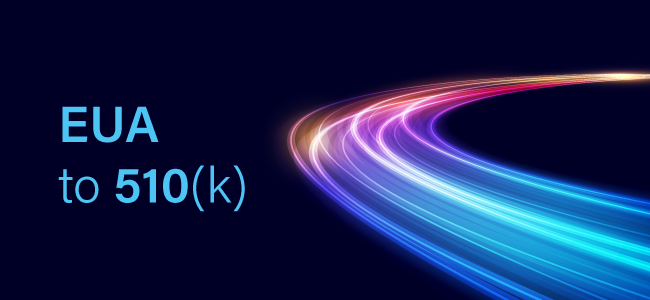
At a glance —
The U.S. Food and Drug Administration (FDA) is ushering companies with EUA products toward a 510(k) submission for clearance.
Triggers increased regulatory obligations, stipulations of 21CFR 820, and a fully compliant Quality Management System (QMS).
You need a system that’s compliant but also works for you and not the other way around.
The elements of a comprehensive QMS encompass a broad spectrum:
- Document, Record & Change Control
- Control of labeling and promotional materials
- Translation of Labeling
- Universal Device Identifier (UDI)
- Personnel Management (Training & Competency)
- Product Development (Design Controls) and Risk Management
- Device Master Record
- Notebook Control
- Purchasing and Supplier Management
- Statistical Techniques
- Process Controls
- Equipment Control
- Production and Quality Controls
- Product Release
- Environmental and Contamination Controls
- Product and Process Change Controls
- Material Control
- Receiving, Handling, and Storage
- Identification and Traceability
- Order Fulfillment and Shipping Controls
- Management Responsibility and Regulatory
- Management Review and Quality Planning
- Registration and Listing
- Reportable Events
- Recalls and Corrections
- Quality Monitoring and Risk Management:
- Corrective and Preventive Action (CAPA)
- Nonconformance Handling
- Deviation
- Complaint Handling and Customer Service
- Post Market Surveillance
- Internal Quality Audits and External Audit Management
Remember, a compliant QMS isn’t one-size-fits-all.
Every company’s fabric is unique, and MDC excels in customizing compliant systems that resonate with your identity, capacity, and purpose.
Let’s carve out a detailed, yet sensible plan that works synergistically with your regulatory strategy, propelling your product’s journey toward 510(k) clearance.
Experience the MDC difference — where regulatory strategy and robust clinical data meet tailored quality solutions.
Let’s pave the way for your success in the dynamic world of diagnostics.